Custom Industrial Blades: A Key to Unmatched Precision and Performance
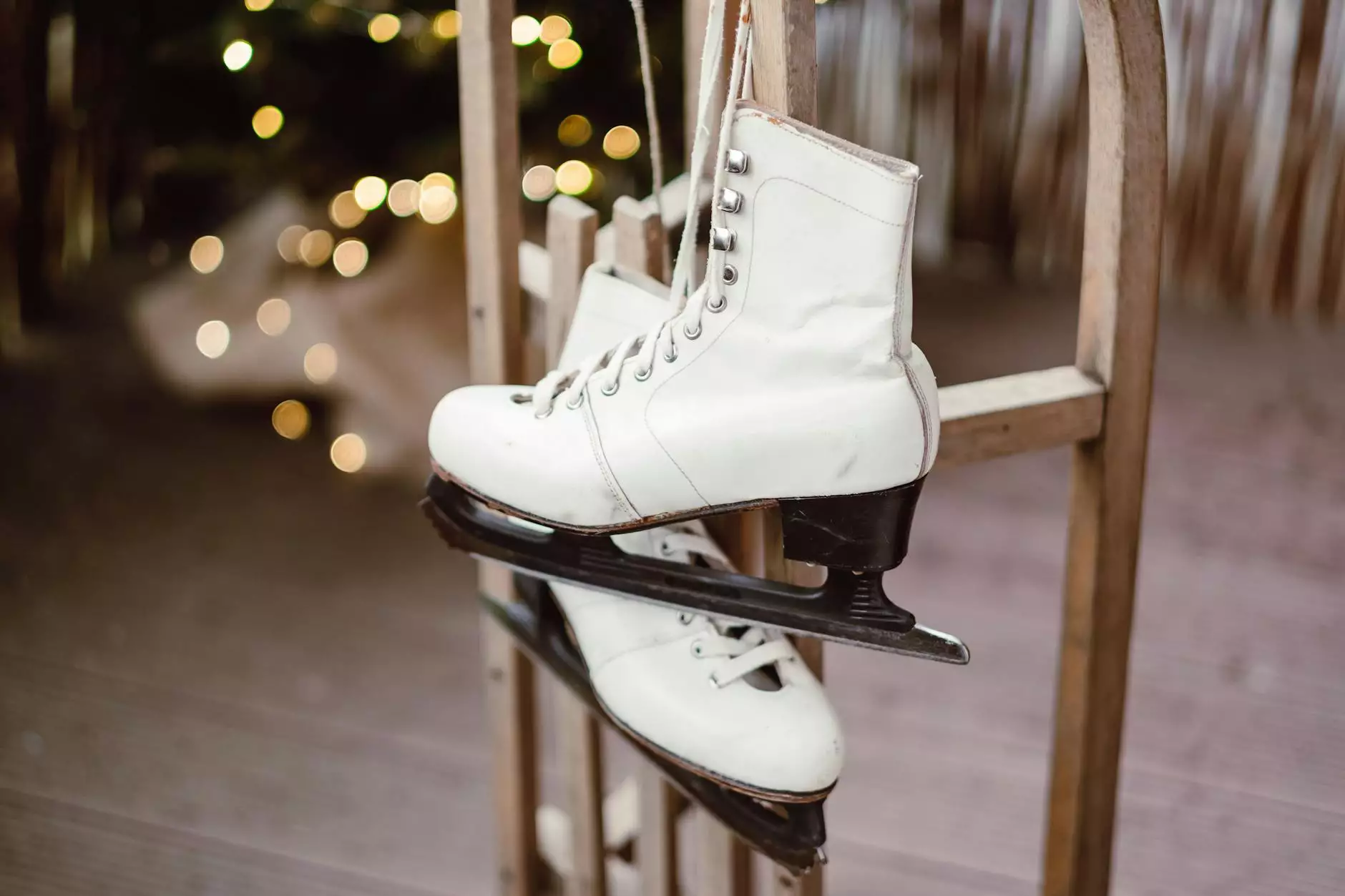
In the modern industrial landscape, having the right tools can significantly influence operational efficiency and productivity. Among these tools, custom industrial blades stand out due to their ability to meet specific needs and applications in various sectors. Whether you are in manufacturing, food processing, or packaging, understanding the benefits of these specialized blades is crucial to elevating your business processes.
Understanding Custom Industrial Blades
Custom industrial blades are precision-engineered cutting tools designed to fit specific applications and industries. Unlike standard blades, which may not cater to unique requirements, custom blades are tailored to meet the exacting demands of specific tasks. This customization can involve variations in blade material, length, width, and blade geometry.
Types of Custom Industrial Blades
There are various types of custom industrial blades, each suited for different industries and applications. Below are some common categories:
- Food Processing Blades: Designed for slicing, dicing, and processing food products with precision.
- Manufacturing Blades: Used in cutting metals, plastics, and composites for manufacturing processes.
- Packaging Blades: Essential for cutting materials used in packaging, such as cardboard and plastic films.
- Woodworking Blades: Specialized for cutting, shaping, and finishing wood products.
- Textile Blades: Custom blades for cutting fabrics with accuracy and minimal fraying.
Advantages of Using Custom Industrial Blades
Choosing custom industrial blades offers numerous advantages that can contribute to your business’s overall efficiency:
1. Precision and Accuracy
One of the primary benefits of using custom blades is the enhanced precision they offer. These blades are designed to meet stringent specifications, ensuring that every cut is made with exacting accuracy. This precision reduces material waste and ensures higher product quality.
2. Increased Efficiency
Custom blades can significantly improve production speed. By optimizing blade designs for specific applications, businesses can reduce downtime associated with blade changes or malfunctions. For instance, a blade that perfectly fits the machine and task at hand can cut through materials faster, leading to quicker production cycles.
3. Cost-Effectiveness
While the initial investment in custom industrial blades may be higher than standard options, the long-term savings often outweigh the costs. By improving longevity, reducing the frequency of replacements, and minimizing material waste, custom blades can lead to significant cost savings over time.
4. Tailored Solutions for Unique Needs
Every industry has its unique challenges. Custom industrial blades can be designed to address those specific challenges, providing tailored solutions that generic blades simply can’t offer. This degree of customization ensures that businesses can achieve operational goals without compromise.
5. Improved Safety Features
Custom blades can also incorporate safety features that are relevant to the specific work environment. By aligning with industry regulations and safety standards, these blades can enhance workplace safety, protecting both the operator and the equipment.
Choosing the Right Custom Industrial Blades
When selecting custom industrial blades, several factors come into play to ensure you make the best choice for your operation. Below are key considerations:
1. Material Selection
The material from which the blade is made has a significant impact on its performance. Common materials include stainless steel, high-speed steel, carbide, and other specialized alloys. Understanding the properties of these materials will help in choosing the right blade for your application.
2. Application Requirements
Identify the specific needs of your application. Consider factors such as:
- The type of material being cut.
- The thickness and hardness of the material.
- The required precision level of the cut.
- The volume of work to be done.
3. Blade Design and Geometry
The design and geometry of the blade play a crucial role in its performance. Factors to evaluate include:
- Number of teeth (for cutting blades).
- Blade thickness.
- Tooth pitch and shape.
- Curvature or straight edges, depending on the intended cut.
4. Manufacturer’s Expertise
Choosing a reputable manufacturer is essential. Look for companies, like SZBlade, that specialize in custom industrial blades, have a strong track record, and can provide references or case studies of their work.
The Importance of Knife Sharpening Services
Alongside the use of custom industrial blades, the maintenance and sharpening of these tools play a pivotal role in ensuring ongoing operational efficiency.
Why Knife Sharpening Matters
Regular sharpening enhances the performance life of a blade, ensuring it maintains its cutting efficacy. Dull blades not only slow down production but can also compromise the quality of the finished product.
Professional Knife Sharpening Services
Engaging professional knife sharpening services ensures that your blades are sharpened to precise specifications that match your operational needs. This concession to quality translates to:
- Increased safety in operations as sharpened blades reduce the risk of accidents.
- Extended blade lifespan, allowing businesses to reduce replacement costs.
- Consistent cutting performance, which is essential for production quality.
Conclusion: Elevate Your Business with Custom Industrial Blades
In the competitive landscape of industry, enhancing operational efficiency is paramount. Investing in custom industrial blades offers a host of benefits, from improved precision and efficiency to reducing overall costs. Coupled with professional knife sharpening services, businesses can optimize their production processes and maintain a competitive edge.
For tailored solutions that meet your unique industry needs, explore the offerings at SZBlade. Our commitment to quality and precision ensures that your cutting tools serve your business effectively, paving the way for success in your operations.